在過去,要獲得一款能夠滿足終端用戶需求、符合所有必需安全和法規標準的可靠配方,需要化學家、技術工程師以及進行客戶試驗的現場服務人員的通力合作。這可能需要幾個月,甚至幾年的時間來不斷完善。
依瑪深知打印品質和減少停機時間對我們的客戶至關重要,因此,我們的大多數墨水和液體產品都在內部開發和制造,以確保我們的設備保持卓越性能。僅在英國,這就意味著我們在利物浦的專業墨水工廠每年生產大約300萬升墨水。
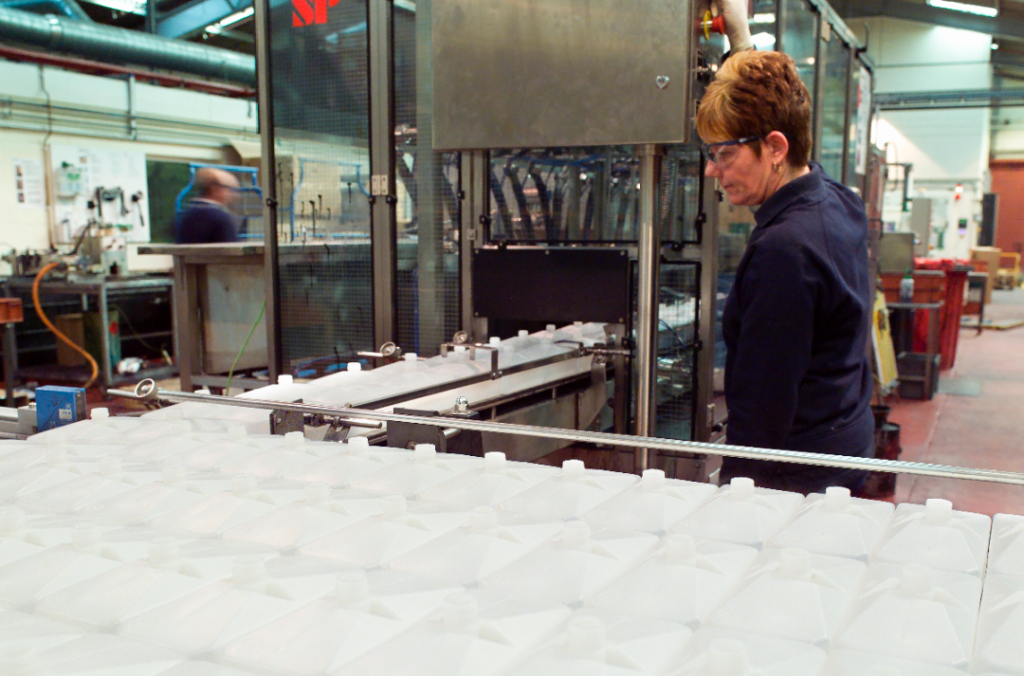
我們還認識到世界發展瞬息萬變,人們現在期望企業能夠在很短時間內創造出同樣卓越質量的產品。因此,我們問自己:如何在加快內部墨水開發的同時確保高質量、高性能的產品,以滿足我們的客戶需求?為了解決這一難題,我們已經開啟了研發工作數字化征程,利用自動化、預測模型和機器學習改進工藝流程,加快各種復雜工作取得進展,達到事半功倍的效果。
01
標準化工藝流程
在實驗室,我們的化學專家通常花費大量時間從事低價值工作,比如稱量材料、混合配方和測試樣品。這些簡單步驟是可以利用數字技術提高生產率的潛在領域。
依瑪投資建設了機器人平臺,能夠處理化學粉末和液體,并根據預先確定的配方混合樣品墨水,減少人工干預。將這部分配方工藝流程自動化后,生產1300多個樣品所需的工作量不到原來的一半,能夠有效地在六個月內完成一年的取樣工作。此外,我們在實驗過程中記錄的化學品使用量減少了57%,隨著我們將更多開發任務轉移到機器人平臺上,這個數字將進一步下降。
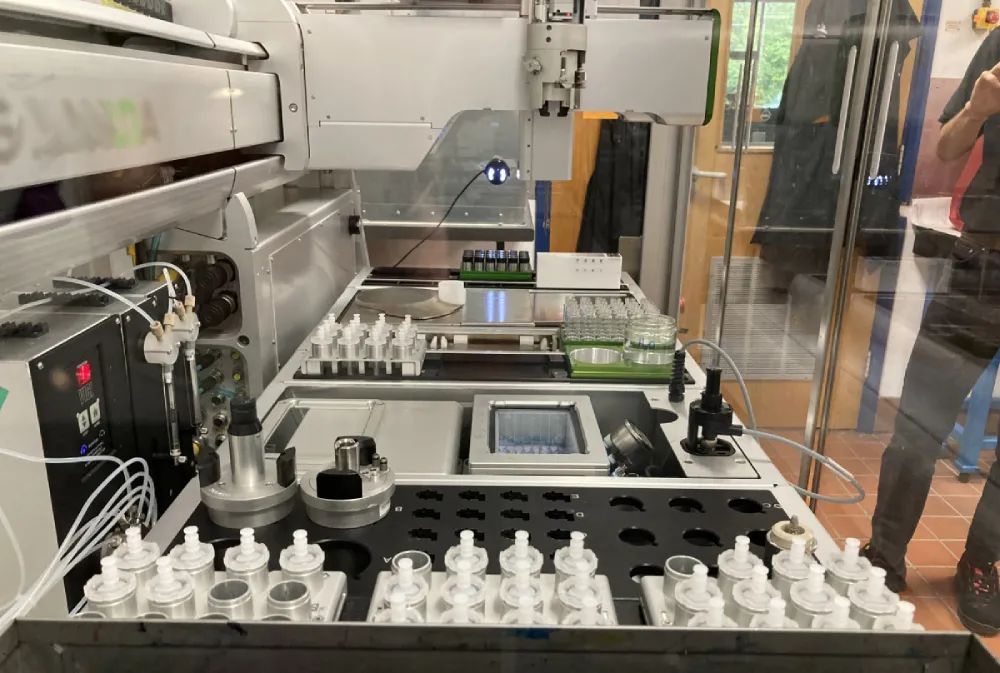
樣品墨水完成配制后,需要測試物理特性,如粘度、密度和電導率。盡管這對配方工藝流程至關重要,但這是可以使用自動化來改進流程、減少浪費并加快開發進度的另一個領域。
我們配備了一套用于測量粘度和電導率的專業設備,從而提高了自動取樣能力。這臺機器可以安排在夜間進行測試,提高可用性,它還可以執行自動清洗,為每個接受測試的樣品節省大約五分鐘。從單個樣本來看,節省的時間并不算多。但從整體角度來說,去年我們測試了4142個粘度樣本和1168個電導率樣本,總共節省了大約450個小時。
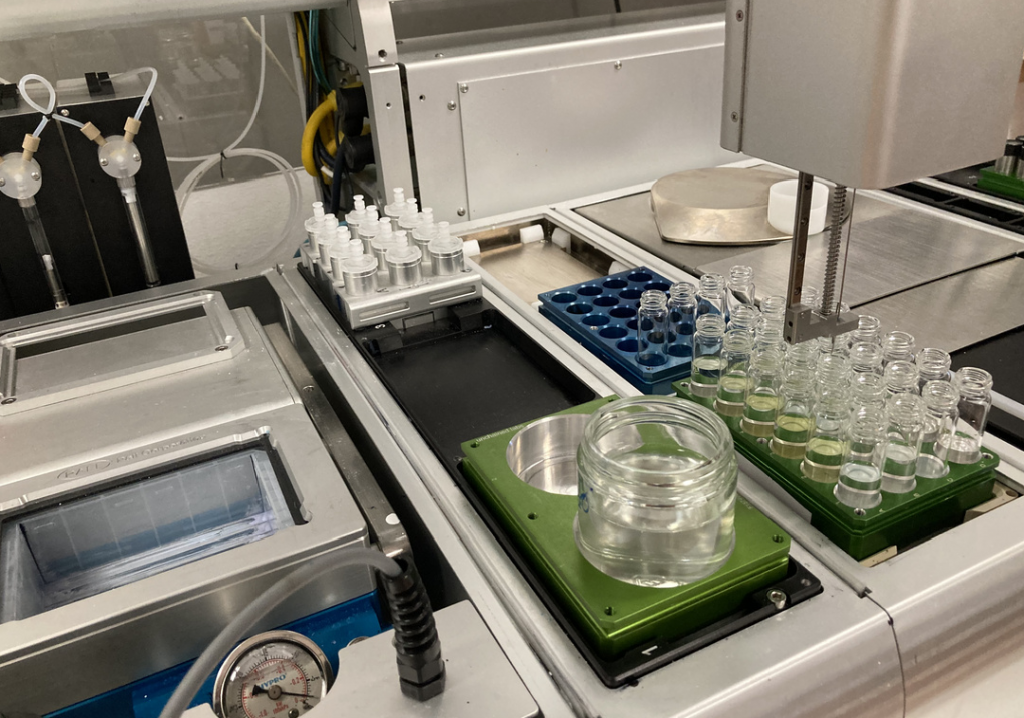
總體上,節省的時間和成本使我們能夠在六個月內償還新設備的成本。新自動化設備精度更高,每個樣品從100克減少到僅8-10克。更少的材料意味降低浪費和成本,而且由于設備可以自己完成清洗,減少了人力和溶劑的使用。清潔功能使溶劑用量減少了80%,在2020年共節省了330升。從生產力、成本和環境的角度來看,這是一個雙贏的結果。
02
預測模型用于加速學習
數據分析是另一個可能從數字化受益的領域。我們開始探索如何使用實驗數據來創建墨水配方的統計數據型設計實驗,即使用統計軟件設計實驗,以確定具有特定特性的樣品墨水配方。
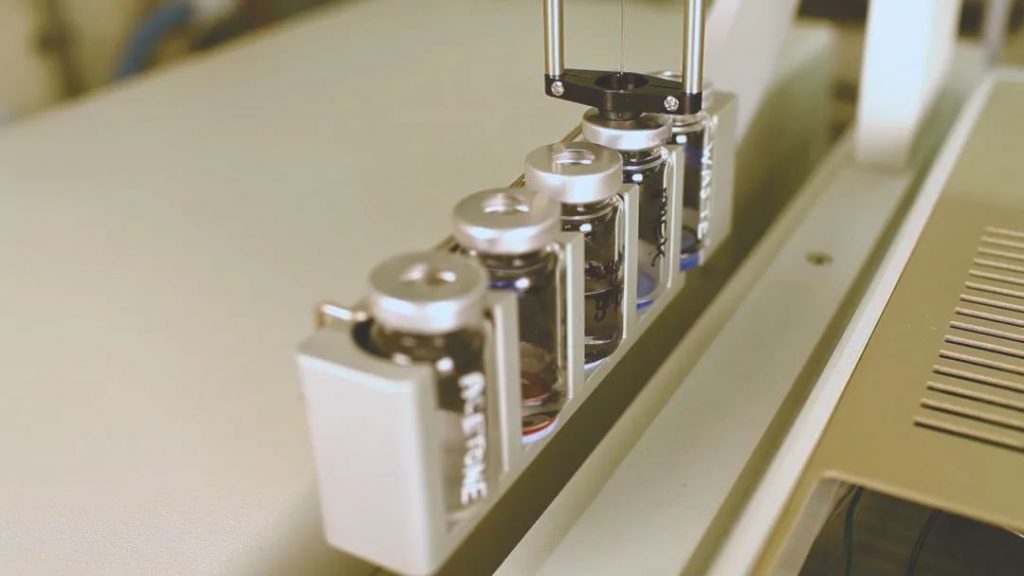
為充分利用化學家在研發實驗室工作中得到的數據,我們定制開發了實驗室電子筆記本。這讓團隊能夠有效地計劃、記錄和訪問關鍵的實驗數據。我們還引入了一些功能,允許團隊查看化學品倉庫中的化學品庫存水平,確保在工作開始前準備好所有材料,減少時間浪費。我們還使用該系統執行和存儲健康和安全評估,評估結果會自動打印在使用的樣品標簽上。
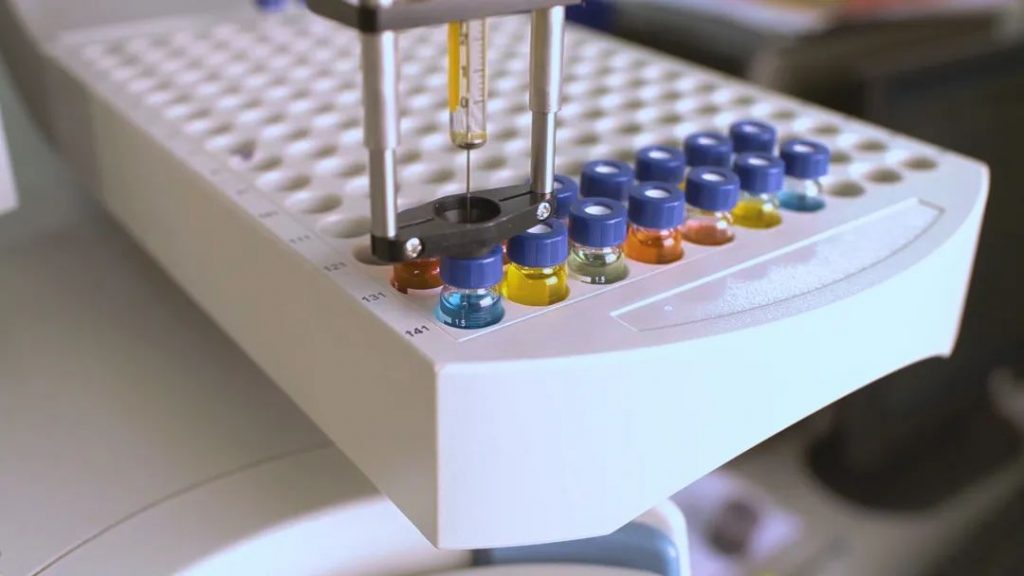
我們使用這些數據作為預測模型的基礎,以識別候選配方,這可以顯著加快采樣工藝流程。
03
使用機器學習的虛擬配方
在這種新方法中,我們還探索了使用數據工程來支持機器學習以確定墨水配方的目標值。如果要生產具有某些性能的墨水,例如柔性薄膜在寒冷環境下的快速干燥時間,我們可以將這些信息輸入機器學習系統,以確定墨水設計的起始假設。該系統還可以幫助我們識別數據中存在的缺陷,并提出改進實驗的建議。
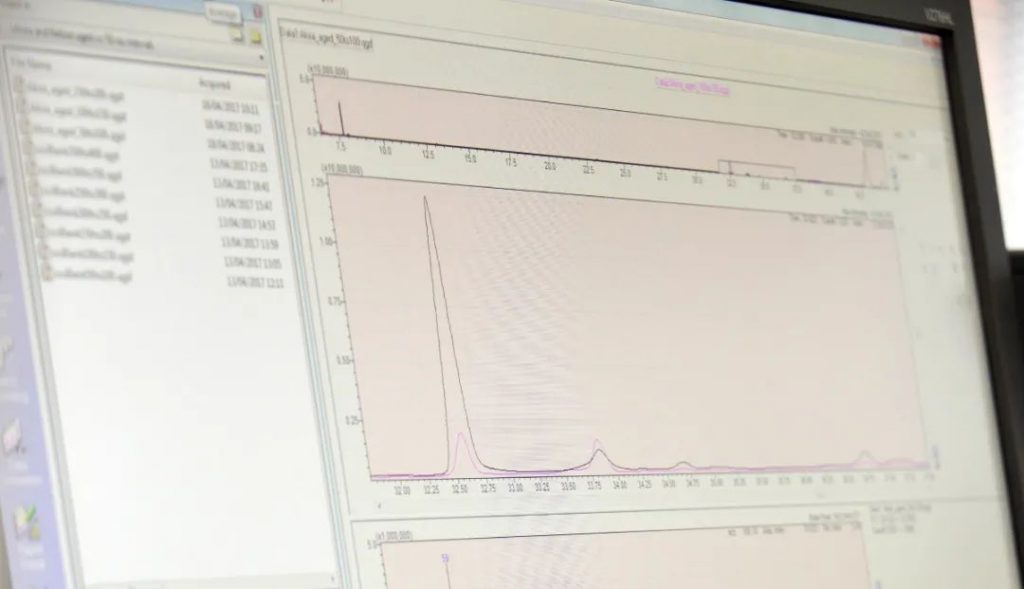
利用電腦進行實驗有助于提高數據質量,并在出現化學品再分類需求時縮短新配方的生產時間。
從可持續發展的角度來看,也有利于減少廢物。進行虛擬再配方時,首先通過電腦開始墨水設計工作,然后再進行實驗室操作,這減少了設計過程中產生的化學廢物總量。
通過自動化配方和測試獲得的結果豐富了設計數據,進而能開展更精確的實驗。這種創新周期使我們能夠以前所未有的速度提供可靠的新型墨水配方,滿足不斷變化的法規要求和客戶需求。
04
未來工作
新工藝流程改進讓研發團隊有更多時間來推動科學和制造創新。我們的化學家現在能夠更好地利用新的培訓機會,并在工作范圍以外的領域開展研究與實驗,比如數據管理和編程等。
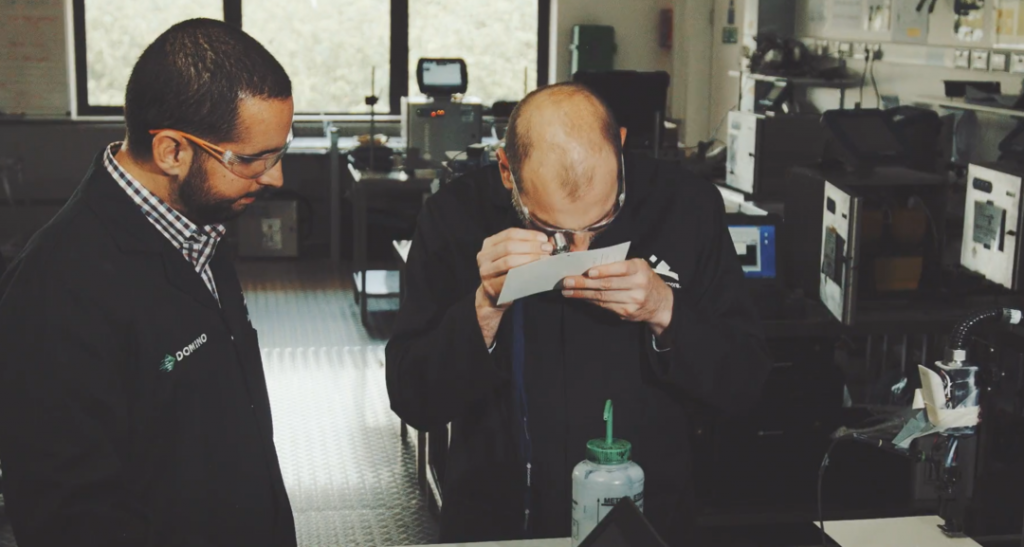
除此之外,我們還著眼于業務之外的領域,例如如何與更廣泛的其他科學界人士合作,以促進創新。最近,某依瑪團隊與劍橋大學制造學院開展合作項目,研究長期困擾連續式噴墨(CIJ)噴碼機的墨水積聚問題。該項目的研究結果將用于未來的預測建模和機器學習活動,以幫助設計更可靠的 CIJ 墨水配方。
依瑪的愿景是培養“未來化學家”,即精通技術,有數字化頭腦,對化學和技術都諳熟于心的專業人士,這個崗位將是我們研發工作的關鍵組成部分。對于如何將數字化流程加入墨水配方流程,出現我們面前的是一個充滿創意的大膽未來。這樣做的好處是縮短了新配方上市的時間,并在可持續性和減少浪費方面取得了進展,而這一切還僅僅是個開始。